This Adjustable Liquor Cabinet is so cool! It’s a great hide-away bar, but also perfect for storage around the house. Let me show you how I made it.
Let’s Build a Liquor Cabinet

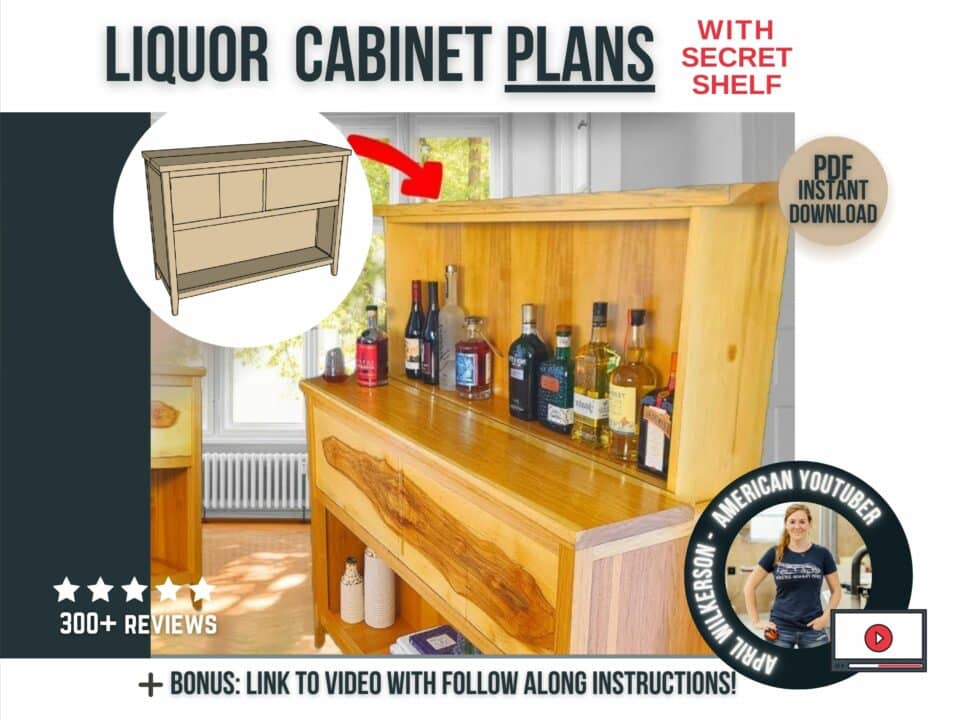
Liquor Cabinet Plans
$9.99
I’ve created a set of liquor cabinet build plans to help you get through the process of building this liquor cabinet.
Materials I Used to Build the Liquor Cabinet
Step 1: Preparing to Make the Moving Portion of the Liquor Cabinet
I made a set of liquor cabinet build plans with a cut list for the liquor cabinet build so I started by cutting the parts needed and milling them to their final dimensions. I labeled all my parts as I made them with a piece of tape so I could pull whichever part was needed as I was moving through the steps.
I’m going to start the assembly by making the shelf portion that will raise and lower with the bottles on it. I grabbed the four solid wood parts needed for the body of this shelf and laid them out. Paying attention to which areas would be seen in the final product and being intentional about the direction it faces.
For joinery on almost this entire build I’m using a simple doweling jig that Rockler makes. After lining up joining boards and drawing pencil marks across the seam, the jig can be clamped into place so that I can drill a hole to the depth needed. You based the depth of the hole off the length of dowels you’re using. There is a collar on the bit that allows you to adjust the depth easily.
This jig works well for boards that are flush with an end but it doesn’t work for boards spaced off the end. For those I used a home made jig and a second collar to make sure I don’t go all the way through the material. You could always do these free hand if you don’t feel like whipping together a jig.

Step 2: Assembling the Moving Shelf
With the holes drilled, now I can assemble it. Remember that you only have a few mins, around 3-5, to get things set in clamps. So I have everything ready; the dowels, a mallet, clamps, and all the parts. When using dowels I always place a small amount of glue in the hole then tap in the dowel. Make sure to not over hit it and distort it’s shape. Then I place glue in the mating part before setting it on the dowel.
If you move things to the ground like me, make sure to lay something down for it to rest on to not mar the surface. Once things were seated all the way, I set a few clamps on it until the glue was dry. Checking for square before walking away from it.

Step 3: Setting the Back of the Shelf in Place
While it sets up, I start drilling in the pocket holes for the plywood panel that will be the back of the shelf. Again, I looked at both sides before drilling any so that I could choose which side would be the final seen face of the final product. I don’t worry about using pocket holes here because it will never been seen. After drilling them all around the perimeter, I set it in place and use screws to attach it.
Then before calling this shelf finished, I add in one more piece of wood. This will later be what rests on the lift so I not only screwed it in place but also used glue. And that is the first big assembly of the build done. I set it aside and started working on the liquor cabinet body.

Step 4: Assembling the Liquor Cabinet Legs
I grabbed what will be the legs and cut in a small taper at the base to create a foot. I like to place an X on the two sides before making any cuts just to make sure my backwards brain doesn’t mix things up. Then I use the Rockler Tapering Jig which easily allows me to chop away the material not needed on two sides.
Ok, that’s the only part that needs something special before building the side assembly, so I grabbed my other parts and started assembling.
Glue Notes:
I always do a dry fit before applying glue. When I do apply glue, I do just a dab. To save on time in the end I actually sand all my parts before assembling them so I do my best to prevent glue squeeze out. A bottle is great for accurately getting glue into the holes but I use a chip brush to get glue on the edges. I also like to have a rubber mallet around to switch over to when things need more force to seat all the way.
If you only have a wooden one, use a scrap piece of wood on your board to prevent it from getting marred. Last thing to think about: you can drastically simplify this project by using pocket holes as the joinery method instead of dowels.
After I made the first, I repeated by making a second side the same way, then also put together the assembly that the lift will later rest on.

Step 5: Joining the Sides of the Shelf
Once dry, I continued building the liquor cabinet body of the cabinet by joining the sides. It is very easy to get things mixed up (it’s a lot of square parts), after I did a dry fit I set out all the parts in their given position and orientation. This way as soon as I started applying the glue I could just run through it.
The first step is pretty easy, applying glue inside each dowel location then tapping in the dowels. The second step is also pretty easy, apply a little glue to the ends of each part and tap it into place. The third step is tricky. There are 14 dowels to get aligned all at the same time and this needs to happen quickly before the glue starts drying. Honestly, it went pretty dang smooth. It’s always a good feeling when things seem to be working. I turned it sideways, complimented it, but then set it in clamps for a few hours to dry.

Step 6: Preparing the Panels for the Other Sections of the Liquor Cabinet
While the body is drying, you can stay busy by cutting all the plywood panels that will go in the different sections. I have all of these on the cut list in my liquor cabinet plans but I cut all of them oversized to start so that I could wait until the body was done and get an exact measurement on what each one needed to be. I again considered the final look I wanted on each panel so I could cut it just so.
To secure these in place, I drilled a few pocket holes on the inside face. Something I do when going into hardwood like the legs here is predrill through the pocket hole to prevent splitting once I run in the screw. It adds time, but nobody wants to split a component at this point.

Step 7: Installing the Center Panel
After getting both side panels in, I repeated with the center panel. This one is slightly tricky because there is no lip for it to rest on. So I grabbed some scrap wood that was the correct height so that I could set the big panel in place while I secured it around the perimeter. I flipped the unit over in order to have better access to the underside to secure the next two panels in place.
Clamping Tip: Clamp a scrap board to the underside of the rails so you do have a flush surface to rest the panel on while securing it.
For the middle shelf, not only is it a slight puzzle to get in…first the shelf, then the clamp can go on, but then I also had to switch to a right angle attachment because of the tight squeeze….but hey! It all worked in the end.
Alrighty, lets flip this liquor cabinet back over and see the progress. My gosh this thing is heavy. Hickory isn’t messing around!

Step 8: Splitting the Top Cubby and Prepping Door Hardware
Up top I put in a few boards that will later give me a surface to attach some door hardware, then I also split the top cubby into two by adding in a center divider. With that in, it’s time for me to work on adding in the rising/lower shelf portion of this build.
I moved back to the shelf assembly I started this build off with and first added in some threaded inserts into the back panel. I did this by counterboring some holes the size of the inserts, then using an Allen to screw them in until flush. The placement of these inserts go with my exact lift, which is a unit made by Progressive Automations. It’s actually marketed as a tv lift so if you wanted to sub this liquor shelf for a TV, you can easily use the plans for a completely different function.
The lift is easily secured down into the support members of the body, then I placed the final back panel in so that I could go to the inside and trace the hole locations with a pencil. After punching through with a drill bit, I could set it back in place then secure it to the lift with bolts. Then go around the boarder and screw in all the pocket holes, making sure the panel was flush.

Step 9: Testing and Adjusting the Moving Pieces
This is the first moving part to test out to make sure things look like they are working and I was very impressed with how quiet it is. What I did was extend the lift all the way up right now, I’ll set the limit later. This way I could grab the shelf and set it on top, using that lip I created earlier, to rest it in place while I secured it with bolts through the threaded inserts I place in the shelf. Then I did the second moving test, which was muuuch more suspenseful. Haha, did I do everything correctly for this shelf to fit inside the body? Lets see.
That front corner rubs slightly but that’s an easy fix. Let me show you the unit from the front as this is where it gets even more exciting. With the body and the shelf working well together, now I need to add on the top but in order for the back to raise and lower independently, I need to have two sections for a top. I start by being selective on wood and grain to come out with the look I will love for the top pieces, and cut it down to size at the table saw. This front section will be fixed in placed, however this back section will be floating and have a small space between the two.
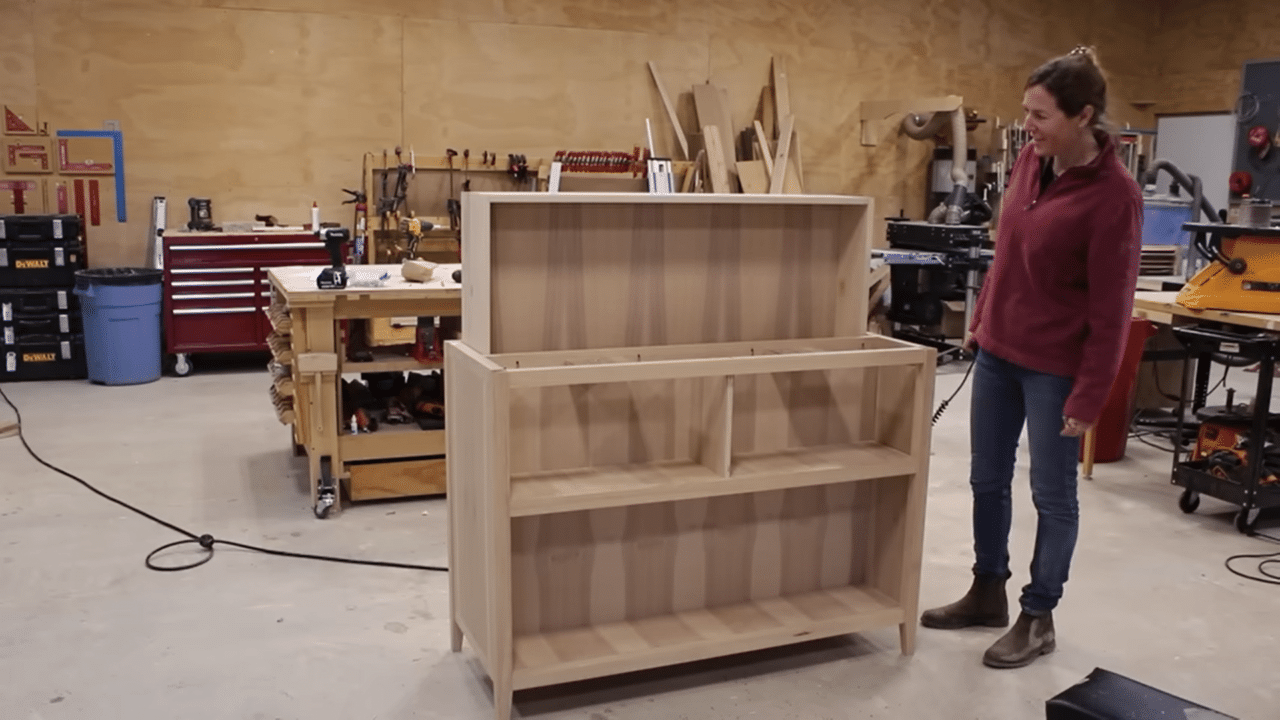
Step 10: Fixing the Front of the Liquor Cabinet
Lets work on fixing the front of the liquor cabinet first. I put an even reveal on all three sides so I used a combination square to make sure it was uniformed, you can see I used a clamp to pin that corner once it was good while I work on adjusting the other side but then I could pin it in place from the underside with pocket holes I drilled in the stretchers before building the frame of the body.
Once that was fixed, I worked on the floating one. This was an experiment, wasn’t sure if it would actually work. What I did was set a collar on a drill bit then counterbore into the body. Here the depth doesn’t really matter, but straightness does. Next, I thread in some screws. I picked screws that had a decent amount of threads but then an unthreaded portion near the top so that after I threaded in the body, I could lop the heads off. I used a grinder for this.
My intention is to create four pins sticking out of the body. I transferred these pin locations to the underside of the floating top section and counterbored more holes. These are just slightly larger than the pins I just placed. The goal is to be able to set the top in place and it not struggle to go on. That’s success one, but success two will be if it goes down without interfering with the fixed front, lets push buttons.
All the successes! Everything works and it feels great. This lift is not only quiet but it’s so stable and smooth on the launch and the landing in both directions. I do have a 5% discount code on the lift columns if you’re needing a lift for an upcoming project. I set the upper limit so that the bottom of the shelf will land flush to the top of the top.

Step 11: Mounting the Liquor Cabinet Doors
I was so happy with how the project worked at this point but I had one more big section to tackle before I was in the clear and that my friends is mounting the doors.
When planning this liquor cabinet project, I wanted a piece of wood that had a ton of contrast, character and visual BAM for these drawer fronts. As you can see, I found the board for me. I waited until this point to cut them so they would be exact to my openings and so I could make it have continuous grain from left to right.
I started by using the Rockler jig again to put a few dowels in that center partition so that I could glue on the portion of solid wood that would cover up the edge. Next I could start attaching the hardware. The right cubby will be a drop down door so I placed two non mortise hinges on the bottom and a catch on the left.

Step 12: Opening the Drawers with a Push
For the catch! I installed something I think is super cool. It’s two parts, here is the body, then here is ball that fits into it’s jaws. When pressed, the jaws close around it. When pressed again, the jaws release it…I took that and turned it horizontal and installed it on the underside of the drawer opening. The tricky part here is getting the depth correct so the door comes out flush to the reveal you’re aiming for. Which in my case is flush to the center partition. I’m dyslexic so any time I get math correct on the first go, I’m super proud and want everybody to see.
I love this mechanism because it means I don’t need to clutter the front with a drawer pull, just a simple push of a finger will open or close the door.
I could have done another drop door on the left however for fun, lets change it to two swing doors. These hinges are mounted on the sides instead of the bottom, then more math to get the hungry hippo openings mounted properly.
Ah. I showed you when I won math, so I’ll show you when I lose. No problem, the hardware is very simple to adjust. Since the left was correct I used a combination square to get the right one set to the same depth. Now lets try that again. That’s more like it!

Step 13: Finishing Touches! Coating the Liquor Cabinet with Wood Finish
Whew, how incredibly satisfying guys! I’ve had this idea for about two years now but I can add things to my list way faster than I can build them, so to see this cabinet complete and working so fabulously, I was on cloud nine. Remember I have a set of plans with all my dimensions, a cut list and even a material shopping list if you’d like to build your own.
Alright, the liquor cabinet build is complete at this point so lastly lets wrap this up with a coat of finish to make it pop and protect it. I am going with one of my favorites which is Gleam by Total Boat. I’m going to go with a three part mash up, where I first apply a coat of Gleams wood sealer. This layer fills the grain, seals wood fibers, and levels the surface to make for an ultra smooth finish.
After I let that dry for two hours, I move on to step two which is Gleam 2.0. I actually want a satin finish as my final look but if you want either a satin or matte final you need to use a Gloss to build up a few layers first. So I laid down three coats of the gloss, waiting an hour in between coats. This stuff dries very fast and evenly so it’s easy to knock out multiple coats in a single day.
Once I got to coat four, I switched over to the Satin. If you’re curious, if you use matte or satin to build up the layers then it can sometimes create a cloudiness. So always use gloss for the build up then use whatever sheen you want as your top layer.
Liquor Cabinet Build Conclusion

When the finish was dry, I moved the liquor cabinet into the house and put everything back together. And wow! What a difference! The table I had here before, was actually one of the first things I ever built but my biggest complaint is I think having all the exposed bottles and mixers on top is just messy looking. I much prefer the prohibition style where it’s sneaky and hidden until you want it exposed.
The Progressive lift comes with a remote on a wire that I velcro to the right side so it’s hidden. With a simple push of a button, the bottles can be raised up. As you can see the lift is so smooth and stable that there is no problem with things moving around and getting broken. I can even place nit nacks on top. In the cubbies I have storage for mixers, accessories, glasses, or even a nice decanter. I love the opening and closing hardware of these doors. Very fun.
I really hope you enjoyed this liquor cabinet build. Don’t forget I have a set of plans, not only for this project but for many others, over on my website. I’ll see you on whatever I’m tackling next.